Habitat For Humanity of Long Island building its first concrete home
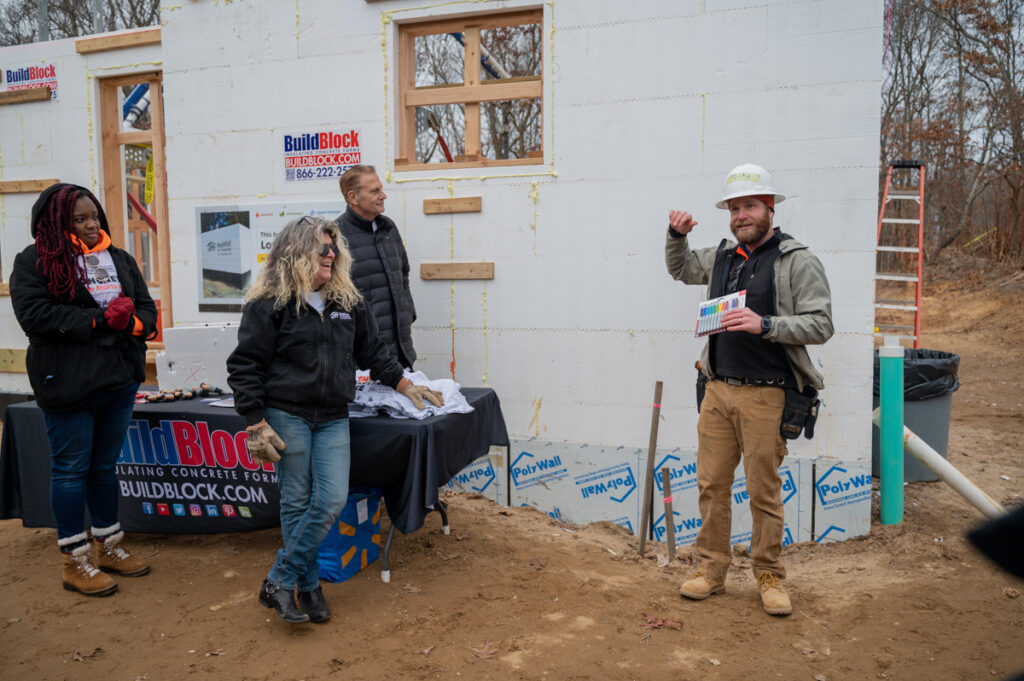
Habitat For Humanity of Long Island held a concrete pouring ceremony Thursday at a build site that marks a first for the local chapter of the nonprofit.
Staffers and volunteers for the organization, which builds affordable housing, are currently building a home at 18 Oak Drive in Riverhead. The 1,044-square-foot, three-bedroom, one-bathroom house is a concrete build-out that utilizes insulating concrete forms (ICF). The technology is an alternative to traditional wooden frames that cuts down on time, labor, costs and materials while increasing sustainability.
Companies like the Oklahoma City-based BuildBlock, which built the ICF materials for the Riverhead home, are members of the National Ready Mixed Concrete Association (NRMCA). The national group, which advocates for ready-mixed concrete as the build of choice, kicked off its Build with Strength campaign to build 50 energy efficient homes in 50 states with Habitat for Humanity International over the next five years.
The NRMCA selected Habitat For Humanity’s Long Island chapter for its New York build. While ICF builds are not new for Habitat For Humanity International, the home at 18 Oak Drive is the Long Island chapter’s first-ever ICF home.
Chris McNamee, Habitat For Humanity of Long Island’s senior director of construction, said she has previously worked with ICF technology. On Monday, she explained, Micah Garrett, BuildBlock’s chief operating officer, educated her Riverhead crew on the materials and process they would use throughout the build. She said her crew had a quick learning curve, and that the organization may utilize ICF again in the future.
“I’ve done this before with a different Habitat in New Jersey, but for basements and crawl spaces, never above ground like this,” she said. “At the end of [this build], I’m going to have a meeting with my whole staff and see … if it was easier for volunteers or more difficult for volunteers. Time-wise, it seems to be quicker so far, it’s very efficient. We’ll have to do a cost comparison, of course, because we fund this with donations, so we have to build as inexpensively as possible to use that donated money as wisely as possible.”
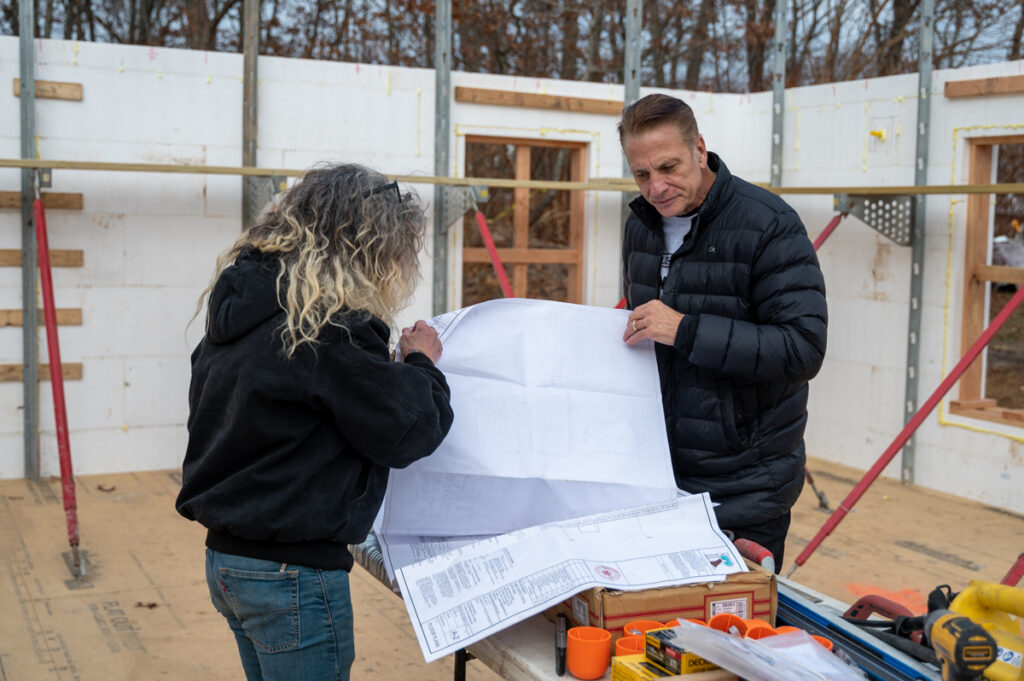
BuildBlock creates stackable ICF blocks into which concrete is poured. As Mr. Garrett put it, the forms are “almost like giant Legos” as they stack easily and quickly. BuildBlock’s molds were used to form the foundation as well as the walls that were built in Riverhead within a week’s time. ICF, Mr. Garrett explained, saves time, money and various materials by cutting out multiple processes in the building of a traditional wood frame home.
“You’re doing multiple steps in the construction process at once,” he explained. “You’re forming, you’re reinforcing, it’s already insulated, it’s furred out, ready for interior and exterior attachment and it’s a vapor barrier at the same time. You cut out all of those additional trades in that process, meaning you basically get all those steps in the construction process done with one crew.”
“This technology has been ongoing — it really took off in the 1980s in the US,” he added. “It’s been around for a long time … But it continues to gain popularity, primarily because we’re able to build structures that are very strong, that are disaster resilient, and we’re able to build structures that are very, very energy efficient. So oftentimes, the people who will live in this home will get a reduction in their energy cost bills, somewhere between 30% to 60%, depending on how the entire structure is built.”
Habitat For Humanity of Long Island received approximately 140 applications for people seeking residency at 18 Oak Drive, representatives for Habitat For Humanity said. The application period for ownership of that home ended Nov. 30. The home’s future occupants have not yet been determined. These homeowners will receive approval for a 30-year mortgage loan through a bank with a 2% interest rate, for which they are responsible for paying 30% of their household income. They must also complete 300 hours of “sweat equity” by helping build their future home or another house in the program, as well as complete budgeting classes and volunteer for community service.
“The heart of the mission is to put a family in this home, to make their dream come true of owning their own home,” Habitat For humanity Long Island CEO Jimmy Jack said while standing on the newly laid floor of 18 Oak Drive. “It’s a united effort to build a beautiful home for a beautiful family.”